Understanding the Crucial Role of a Titanium Fasteners Factory in Modern Industries
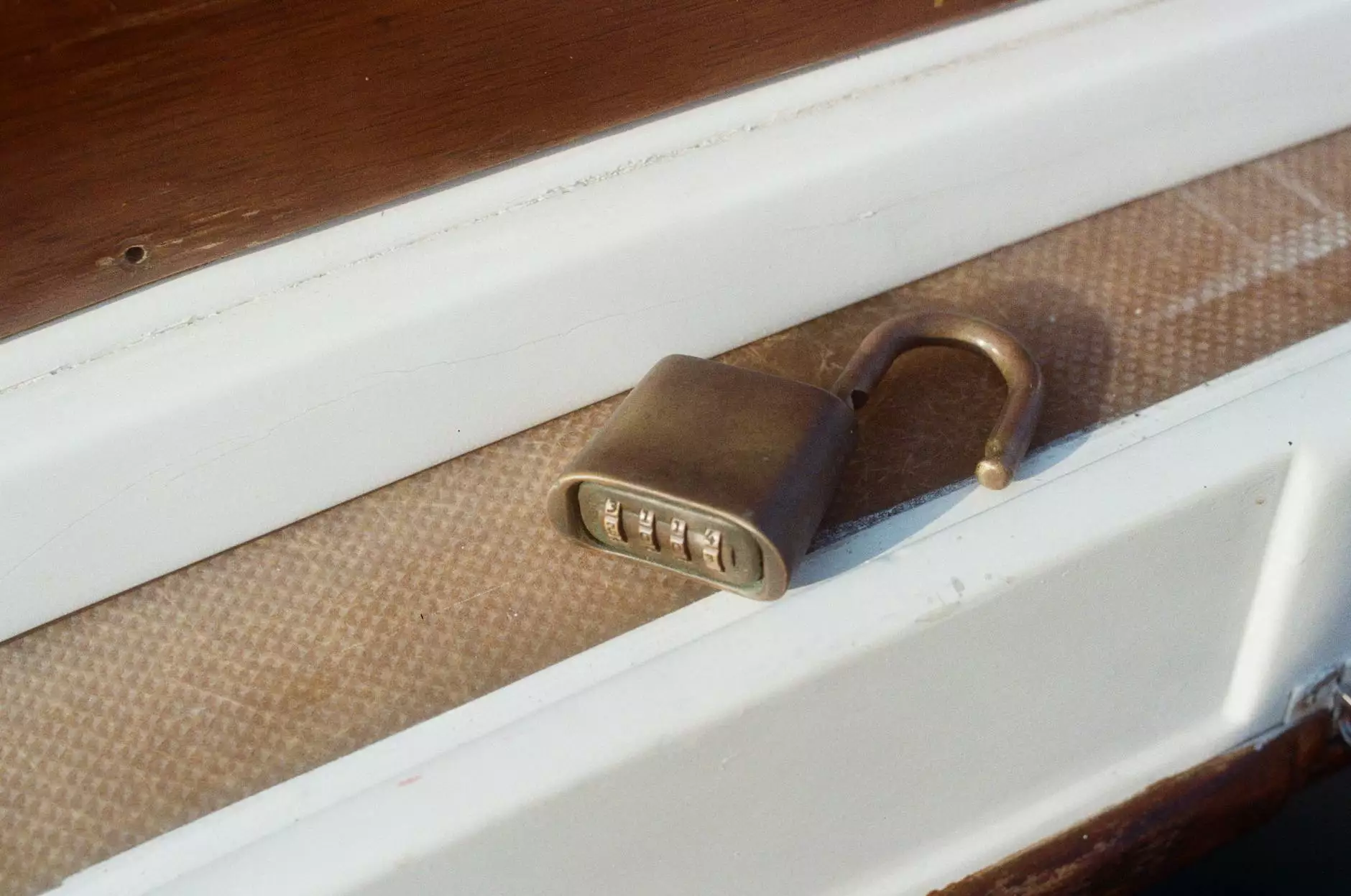
Titanium fasteners have emerged as one of the most sought-after components in various sectors, including aerospace, automotive, marine, and construction. As industries evolve and demand high-performance materials, the importance of a titanium fasteners factory cannot be underestimated. This article explores the nuances of these specialized factories, the benefits of titanium fasteners, and their applications in various fields.
What Are Titanium Fasteners?
Titanium fasteners are hardware components made from titanium or titanium alloys, designed to join, secure, or attach various parts in an assembly. They include:
- Bolts
- Nuts
- Screws
- Washers
- Studs
Known for their high strength-to-weight ratio and excellent corrosion resistance, titanium fasteners play a pivotal role in enhancing the durability and performance of industrial products. The manufacturing processes used in a titanium fasteners factory leverage advanced technology to ensure precision and quality.
Why Choose Titanium Fasteners over Traditional Materials?
The transition to titanium fasteners from traditional materials such as steel or aluminum is driven by several compelling factors:
1. Strength and Weight
Titanium fasteners provide exceptional strength while being significantly lighter than their steel counterparts. This feature is particularly advantageous for industries where weight savings translate to improved performance and efficiency.
2. Corrosion Resistance
One of the standout properties of titanium is its natural resistance to corrosion, making it ideal for use in harsh environments, including marine and chemical processing applications. Unlike steel, which can rust and degrade, titanium remains stable over time.
3. High-temperature Performance
Titanium fasteners can withstand high temperatures, making them suitable for applications in aerospace and automotive industries, where heat resistance is crucial for safety and performance.
4. Biocompatibility
The biocompatibility of titanium makes it an excellent choice for medical applications. In the titanium fasteners factory, products designed for the medical field must meet stringent quality standards and specifications.
The Manufacturing Process in a Titanium Fasteners Factory
The manufacturing of titanium fasteners involves several intricate steps that ensure each product meets the highest quality standards. The following outlines the typical processes involved:
1. Material Selection
The first step in the manufacturing process is selecting high-purity titanium or titanium alloys. Common grades include Ti-6Al-4V, known for its excellent strength and corrosion resistance, and commercially pure titanium, which offers great workability.
2. Melting and Forging
Titanium is typically melted in an inert atmosphere to prevent oxidation. After melting, the titanium is forged into bars or billets, creating intermediate shapes that can be further processed.
3. Machining
The machined components are crafted from forgings or bar stock to create precise fasteners. CNC (Computer Numerical Control) machining is frequently used in a titanium fasteners factory to achieve tight tolerances and a high-quality finish.
4. Heat Treatment
Heat treatment processes may be applied to enhance the mechanical properties of the fasteners. This step is crucial, especially for fasteners expected to endure extreme conditions.
5. Surface Treatment
Surface treatments such as anodizing or coating can be applied to further enhance corrosion resistance and durability. These treatments also improve the aesthetic appearance of the fasteners.
6. Quality Control
Rigorous testing is conducted at various stages of production to ensure each fastener meets industry standards and client specifications. This may include mechanical testing, metallographic analysis, and non-destructive testing methods such as X-ray inspection.
Applications of Titanium Fasteners Across Industries
Titanium fasteners are versatile and find applications in numerous industries. Here are some of the key sectors where they are employed:
Aerospace Industry
The aerospace sector relies heavily on titanium fasteners due to their lightweight and high strength. They are used in airframes, engines, and landing gear components to enhance overall performance and reduce weight.
Automotive Sector
High-performance vehicles use titanium fasteners to reduce weight while maintaining safety and durability. They are found in engine components, suspension systems, and exhaust systems.
Marine Applications
In marine environments, the resistance of titanium to saltwater corrosion makes it perfect for use in shipbuilding, fishing equipment, and offshore platforms, ensuring longevity and reliability.
Medical Devices
Titanium fasteners are often included in surgical implants and medical devices due to their biocompatibility and strength. They are used in joint replacements and dental applications.
Construction Industry
The construction industry increasingly uses titanium fasteners for structural applications due to their durability and resistance to corrosive environments, which is especially important in coastal areas.
The Environmental Impact of Titanium Fasteners
In an era where sustainability is paramount, the environmental impact of materials and manufacturing processes is more important than ever:
1. Recyclability
Titanium is 100% recyclable, making it an environmentally friendly choice for fastener production. Companies engaged in titanium fasteners manufacturing can significantly reduce their carbon footprint by implementing recycling programs.
2. Reduced Waste
Advanced manufacturing techniques employed in titanium fasteners factories contribute to reduced waste generation, as modern technologies allow for precision manufacturing that minimizes scrap materials.
Conclusion
As we explore the future of materials in various industries, the role of a titanium fasteners factory is becoming increasingly crucial. With their superior properties, titanium fasteners are revolutionizing the way we think about fastenings in high-demand applications.
Investing in titanium fasteners translates not just to improved product performance but also to long-term reliability and sustainability. As industries continue to innovate, the demand for high-quality titanium fasteners will only grow, making titanium fasteners factories vital allies in this ongoing journey of industrial advancement.
Final Thoughts on Partnering with a Titanium Fasteners Factory
For businesses seeking quality titanium fasteners, it’s essential to partner with a reputable titanium fasteners factory such as titaniumbolts.com. Reliable suppliers not only ensure top-grade products but also provide valuable insights into the latest innovations and industry trends.
In conclusion, the future is bright for titanium fasteners, and as industries evolve, they will undoubtedly play a larger role in shaping modern engineering solutions. Together, let's embrace the potential of titanium and drive forward into a new era of industrial excellence.